Packaging Machine Repair Service: Avoid Costly Malfunctions with Professional Assistance
Packaging Machine Repair Service: Avoid Costly Malfunctions with Professional Assistance
Blog Article
Comprehending the Secret Elements and Repair Work Techniques for Packaging Maker Maintenance
Effective upkeep of product packaging machines rests on a complete understanding of their vital parts, consisting of the frame, drive system, and securing mechanisms. Recognizing typical upkeep issues, coupled with the implementation of preventative approaches and fixing methods, can substantially boost machine reliability. Furthermore, the selection of repair work practices, including the usage of OEM components and the importance of licensed technicians, plays a vital duty in minimizing downtime. To truly understand the complexities of these systems and their upkeep, one should think about the more comprehensive ramifications of overlooking these important techniques.
Key Components of Packaging Equipments
Product packaging machines contain a number of crucial elements that collaborate to ensure reliable and effective packaging processes. At the core of these devices is the framework, which gives architectural stability and houses the numerous operating components. The drive system, frequently a mix of electric motors and gears, helps with the motion of parts, enabling accurate procedure throughout the product packaging cycle.
An additional vital element is the conveyor system, which moves products through different stages of the packaging process. This is usually matched by sensing units and controls that keep track of the placement and speed of products, making certain synchronization and decreasing mistakes. The loading system is critical for properly dispensing the ideal amount of product into bundles, whether in fluid, powder, or strong type.
Sealing devices, consisting of heat sealants or glue applicators, play an essential function in safeguarding packages, avoiding contamination and expanding service life. In addition, labeling systems are important for giving necessary product info, guaranteeing compliance with laws. The control panel, outfitted with straightforward interfaces, allows operators to manage maker functions, screen efficiency, and make modifications as required, making sure optimal performance and performance in product packaging operations.
Common Upkeep Problems
Effective procedure of product packaging makers relies heavily on routine maintenance to prevent common concerns that can interfere with manufacturing. Amongst these problems, mechanical wear and tear is prevalent, particularly in parts like motors, conveyors, and seals, which can lead to unanticipated downtimes. Additionally, misalignment of parts can cause inefficient operation, triggering items to be inaccurately packaged or harmed during the process.
One more common upkeep issue includes the build-up of dust and debris, which can conflict with the machine's sensing units and moving components. packaging machine repair service. This not only affects performance but can likewise position safety and security risks. Additionally, lubrication failings can bring about raised friction, leading to getting too hot and ultimate part failure.
Electric issues, usually originating from loosened connections or worn-out electrical wiring, can disrupt equipment features, bring about substantial manufacturing delays. Lastly, software glitches because of obsolete programs or inappropriate configurations can impede the device's operation, requiring prompt intervention. Resolving these typical upkeep problems proactively is necessary for guaranteeing ideal efficiency and longevity of packaging equipment.
Preventative Maintenance Approaches
Carrying out preventative maintenance techniques is vital for maintaining the efficiency and dependability of packaging equipments. These approaches encompass a systematic method to maintenance, view it concentrating on the regular evaluation and maintenance of devices to preempt prospective failings. By adhering to an arranged maintenance program, drivers can identify deterioration on parts prior to they result in significant breakdowns.
Trick elements of a preventative maintenance method include routine evaluations, lubrication, cleansing, and component replacements based upon maker referrals. Making use of checklists can improve this process, making certain that no important tasks are ignored. In addition, keeping exact records of upkeep tasks aids in tracking the maker's efficiency gradually, helping with notified decision-making regarding future upkeep demands.
Educating team on the significance of preventative upkeep enhances compliance and cultivates a society of aggressive care. Applying an anticipating maintenance element, utilizing information analytics and sensor technology, can better enhance machinery performance by forecasting failings prior to they happen.
Troubleshooting Techniques
When faced with malfunctions or inefficiencies in product packaging devices, employing organized troubleshooting strategies is essential for determining and solving concerns quickly. The initial step in efficient troubleshooting is to develop a clear understanding of the machine's functional specifications and performance metrics. This involves examining the machine's specs, in addition to any type of error codes or alerts presented.
Following, drivers should perform a visual evaluation, inspecting for noticeable indicators of imbalance, damages, or wear. This usually includes examining gears, belts, and sensing units to identify potential root causes of malfunction. Gathering operational information, such as manufacturing prices and downtime logs, can also supply insights right into reoccuring issues.
As soon as potential troubles are recognized, making use of a rational technique to isolate the source is vital. This may need testing individual parts or systems in a regulated fashion. Participating in conversations with operators that interact with the machinery consistently can produce valuable feedback about uncommon habits or patterns.
Repair Service and Substitute Finest Practices
A detailed understanding of fixing and substitute best techniques is important for preserving the durability and effectiveness of product packaging equipments. Frequently assessing the condition of machine components permits prompt treatment, preventing even more substantial problems pop over to these guys that can cause expensive downtimes.
When repairs are essential, it is necessary to use OEM (Original Tools Supplier) parts to guarantee compatibility and efficiency. This not only protects the honesty of the equipment however also upholds service warranty contracts. Furthermore, it is advisable to reference preserve an inventory of important extra components to promote quick substitutes and reduce operational interruptions.
For complicated repair services, engaging qualified technicians with specialized training in packaging equipment is advised. They have the proficiency to diagnose concerns properly and implement repairs effectively. Documenting all repair work tasks and parts replacements is essential for keeping a thorough maintenance background, which can help in future troubleshooting.
Lastly, executing an aggressive technique, including regular evaluations and anticipating maintenance methods, improves the dependability of product packaging equipments. By adhering to these ideal techniques, organizations can guarantee optimal equipment efficiency, lower operational risks, and prolong devices lifespan.

Verdict
In final thought, a detailed understanding of product packaging equipment parts and efficient upkeep methods is important for optimum performance. By implementing these techniques, companies can guarantee the longevity and efficiency of product packaging makers, ultimately contributing to enhanced operational efficiency and reduced costs (packaging machine repair service).
Effective maintenance of product packaging devices pivots on a comprehensive understanding of their essential components, including the framework, drive system, and securing devices.Effective procedure of product packaging devices depends heavily on normal upkeep to prevent common issues that can disrupt manufacturing.Executing preventative upkeep approaches is important for maintaining the effectiveness and reliability of packaging devices. In addition, maintaining accurate documents of upkeep activities help in tracking the device's performance over time, facilitating informed decision-making regarding future upkeep demands.
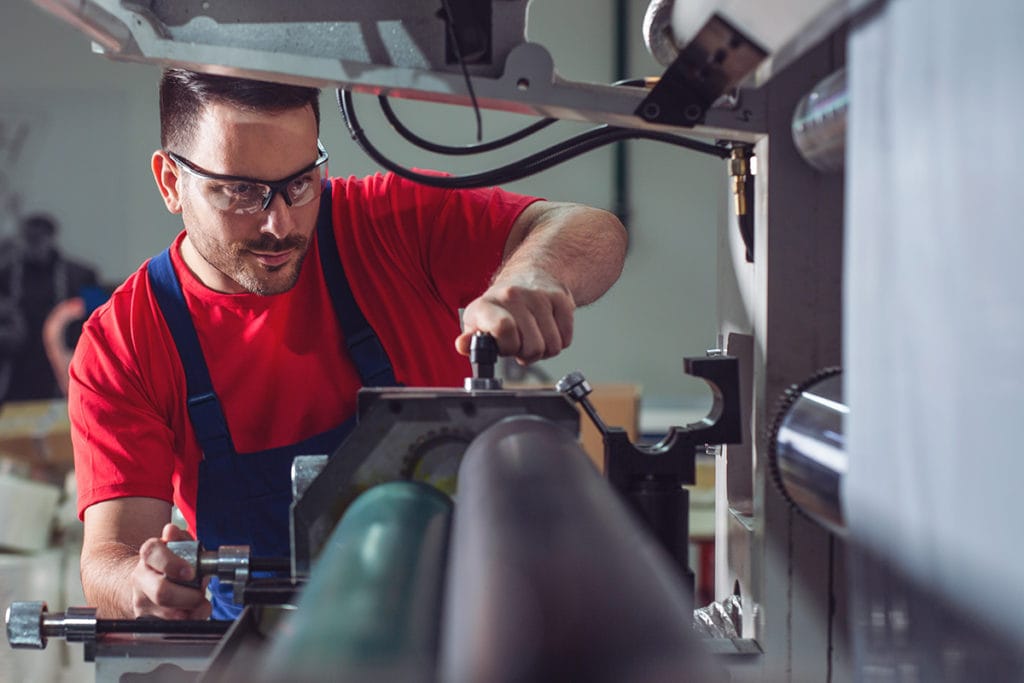
Report this page